Railcar Health Basics: Contract vs. Running Repairs
Maintaining your railcar fleet’s health is crucial for smooth operations and minimizing costly disruptions that can throw a wrench in your logistics. Understanding the different types of railcar repairs, specifically running and contract repairs, can help you make informed decisions that optimize your railcar maintenance strategies. In this blog, we'll delve into the nuances of these repair types, guided by the Association of American Railroads (AAR) rules, and highlight the importance of proactive monitoring for railcar health.
Types of Railcar Repairs and Their Importance
AAR Rules Governing Railcar Repairs
Running Repairs: What They Are, Pros & Cons
What Are Running Repairs?
Pros of Running Repairs:
- Immediate Action: Addressing safety issues promptly ensures the railcar can continue its journey without significant delays.
- Minimal Downtime: On site repairs prevent extended downtime, keeping freight moving smoothly.
- Streamlined Process: Railroads have complete control over the repair process, eliminating the need for approval delays.
Cons of Running Repairs:
- Higher Costs: Running repairs are billed at AAR rates, which are typically more expensive than contract shop repairs.
-
Limited Control: Car owners have no say in the components or repair methods, which might not align with their preferences and can lead to unexpected outcomes.
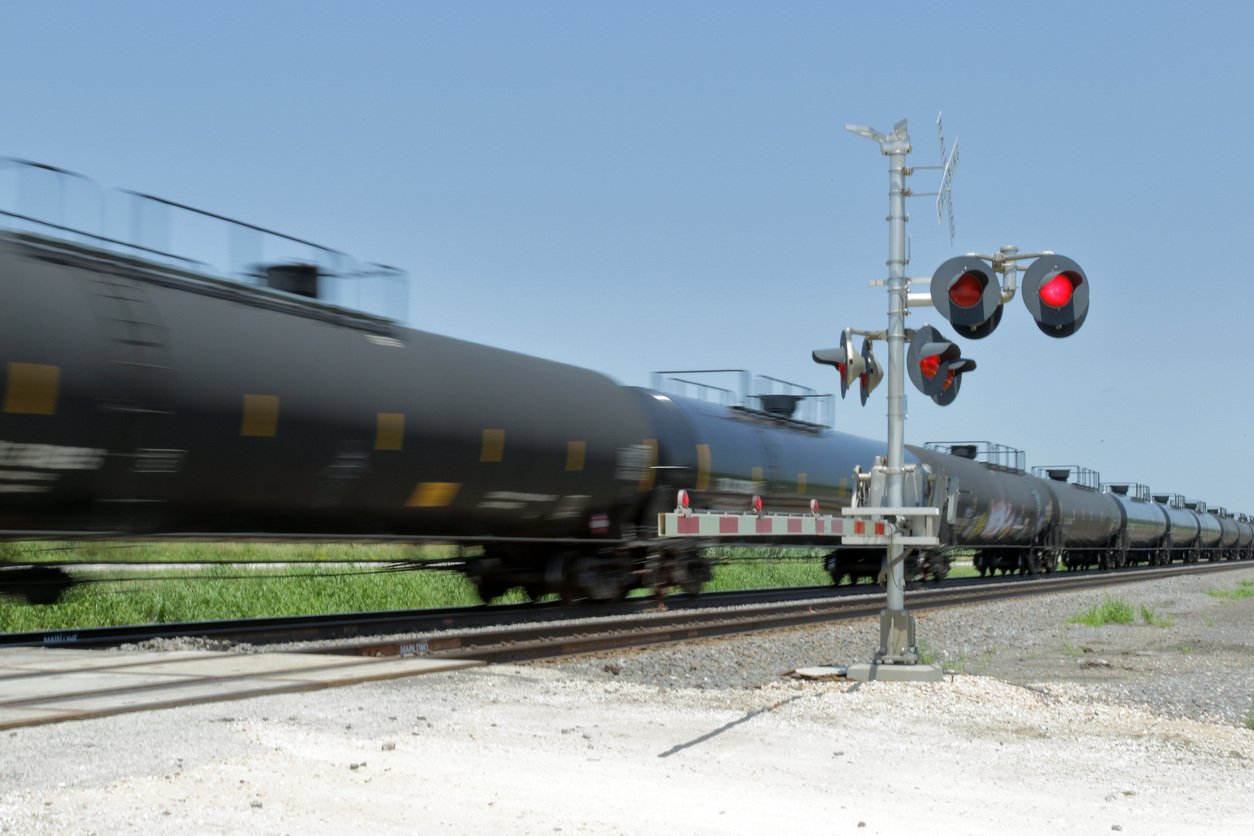
What Are Contract Repairs?
Pros of Contract Repairs:
- Cost-Effective: Contract repairs are typically cheaper than running repairs, as they are not subject to AAR rates.
- Owner Control: Car owners can specify the components used and request additional maintenance tasks, optimizing the repair process.
- Work Grouping: Combining multiple repair tasks can save on transportation costs and reduce repeated trips to the shop.
Cons of Contract Repairs:
- Routing Costs: Transporting a railcar to a contract shop incurs additional costs and time.
- Approval Delays: The need for owner approval can delay the initiation of repairs, potentially leading to extended downtimes.
Importance of Proactive Railcar Health Monitoring
Benefits of Proactive Monitoring:
- Cost Savings: Addressing issues early can prevent more extensive and costly repairs.
- Reduced Downtime: Proactive maintenance helps avoid unexpected service disruptions and delivery delays.
- Efficient Fleet Management: Identifying opportunities for work grouping minimizes the time railcars spend out of service.
Getting Proactive
Achieve peace of mind with a proactive maintenance plan using the TransmetriQ Platform. Our advanced tools and monitoring systems help keep your fleet in peak condition, reducing disruptions and enhancing operational efficiency. Discover how we can help optimize your railcar health management by exploring the full capabilities of the TransmetriQ Platform or contact our team for personalized support.